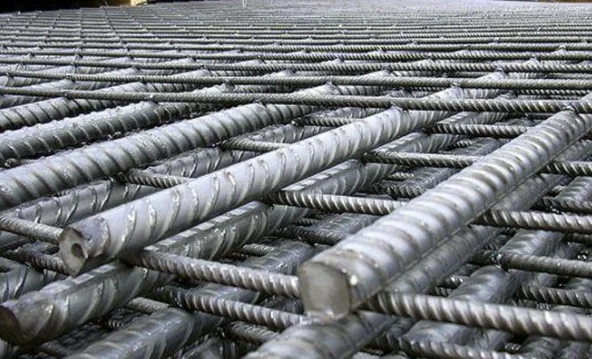
Bar Bending Schedule And Pre Cut Bend Steel In Concrete
Jan 21, 2025Bar Bending Schedule and Pre-Cut Bend Steel in Concrete Construction Projects
Bar Bending Schedule and Pre Cut Bend Steel in Concrete Construction Projects
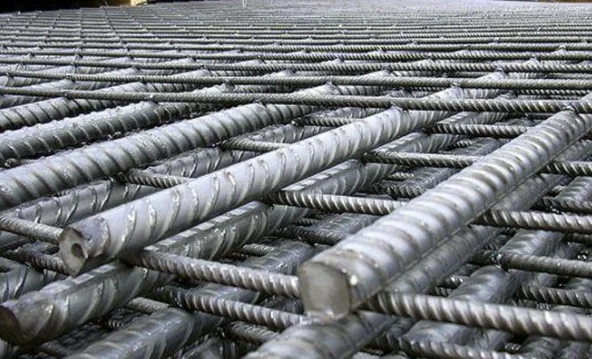
I. Introduction
What is a Bar Bending Schedule (BBS)?
In the concrete construction industry, precision matters. A Bar Bending Schedule (BBS) serves as a detailed chart that outlines every reinforcement bar—commonly referred to as rebar—required for a structure. It specifies the size, shape, length, and quantity of these bars to ensure the construction aligns with design specifications. Think of it as a detailed guide that ensures accuracy in cutting and bending steel, optimizing both time and resources.
The Concept of Pre-Cut and Bent Steel
Pre-cut and bent steel revolutionizes this process by preparing the rebar off-site based on the BBS. Delivered ready for placement, these pre-fabricated bars reduce on-site labor and improve efficiency. With growing popularity in modern construction, this method ensures accuracy while cutting down costs and time.
II. Importance of Bar Bending Schedule in Construction
Standardization and Accuracy
BBS ensures each rebar is cut and bent precisely to design specifications. This eliminates guesswork and minimizes errors, ensuring the structure’s safety and compliance with design standards.
Efficiency and Cost Savings
A well-prepared BBS reduces waste by specifying exact material requirements. This minimizes over-ordering and leads to significant cost savings. Clear instructions in the BBS also expedite construction timelines, helping projects meet deadlines more effectively.
Quality Assurance
When rebar is fabricated and placed correctly, it directly impacts the structure’s durability and strength. A BBS plays a critical role in maintaining high-quality construction standards by reducing the scope for manual errors.
III. Components of a Bar Bending Schedule
Key Elements
A typical BBS includes:
-
Bar Number: Unique ID for each piece of rebar.
-
Shape: Required geometry (e.g., straight, bent, or hooked).
-
Size: Diameter of the bar, usually in millimeters.
-
Length: Exact measurement.
-
Quantity: Number of bars needed.
-
Bar Type: Whether it’s a main bar, stirrup, or distribution bar.
-
Shape Codes: Standardized codes describing bending dimensions and angles.
Shape Photos:
These photos can be used in an excel file or a word file to illustrate the shapes of different types of steel reinforcement cut and bend. the table in the excel file is called Bar Bending Schedule with abbreviation of B.B.S.
Interpreting a BBS
Presented in a tabular format alongside structural drawings, a BBS ensures every bar is fabricated and placed as per design, enhancing workflow accuracy and efficiency.
Sample Bar Bending Schedule
Bar No. | Shape | Bar Size (mm) | Length (mm) | Quantity | Shape Code |
---|---|---|---|---|---|
1 | Straight | 12 | 6000 | 10 | 00 |
2 | L Shape | 16 | 2000 + 1000 | 8 | 01 |
3 | U Shape | 10 | 1500 + 500 + 1500 | 6 | 02 |
4 | Hooked End | 20 | 3000 | 12 | 03 |
5 | Stirrups (Square) | 8 | 500 x 500 | 20 | 04 |
IV. Pre-Cut and Bent Steel: A Game-Changer
Definition and Process
Pre-cut and bent steel is fabricated in specialized facilities using advanced machinery. Engineers feed BBS data into software, guiding machines to cut and bend bars precisely. These labeled bars are then delivered to the site for immediate use.
Advantages
-
Reduced On-Site Labor: Workers focus on placement instead of fabrication.
-
Enhanced Precision: Automation ensures exact specifications.
-
Time Savings: Eliminates on-site cutting and bending.
-
Improved Safety: Minimizes risks associated with manual processes.
Challenges
-
Dependence on Accurate Designs: Errors in BBS can disrupt fabrication.
-
Logistics: Transporting pre-fabricated steel requires careful planning.
-
Higher Initial Costs: Though initially more expensive, savings in time and labor offset the costs.
V. Comparison: Traditional Steel vs. Pre-Cut and Bent Steel
Time Efficiency
Traditional methods rely on on-site cutting and bending, often leading to delays. Pre-cut steel eliminates these steps, ensuring faster installation.
Material Optimization
Pre-cut steel reduces material waste by adhering to exact specifications, unlike traditional methods prone to errors and offcuts.
Cost Implications
While pre-cut steel may have a higher upfront cost, it reduces overall expenses by saving on labor and shortening construction timelines.
VI. Role of Technology in BBS and Pre-Cut Steel
Digital Tools
Software like AutoCAD and Revit streamline BBS preparation and integrate with automated machines for precise fabrication, reducing errors.
Integration with Pre-Cut and Bent Steel
Digital workflows between design tools and fabrication equipment ensure efficient and accurate manufacturing of steel bars.
Emerging Trends
Technologies like Building Information Modeling (BIM) and 3D printing are shaping the future of rebar design and fabrication, promising even greater efficiency.
VII. Practical Applications in Construction Projects
Examples of Structures Using BBS and Pre-Cut Steel
-
Skyscrapers.
-
Bridges and flyovers.
-
Large-scale industrial facilities.
Case Study
A high-rise project that implemented pre-cut steel and BBS saw a 30% reduction in construction time and a 20% cut in material costs. This example highlights the benefits of adopting these modern practices.
VIII. Conclusion
Summarizing Benefits
Bar Bending Schedules and pre-cut steel enhance efficiency, improve safety, and ensure superior quality in construction projects. Together, they simplify workflows and optimize resource utilization.
Future Outlook
As construction embraces technology, the use of BBS and pre-cut steel will grow. Sustainability efforts, like recycling steel waste, will further drive adoption, cementing their role in modern construction.
VIX. Downloads
Download sample excel and pdf formats:
- Download the excel format for bar bending schedule (BBS) sample for steel reinforcement
- Download PDF format for bar bending schedule (BBS) sample for streel reinforcement
References:
Quollnet.com specialized developers for engineering IT products